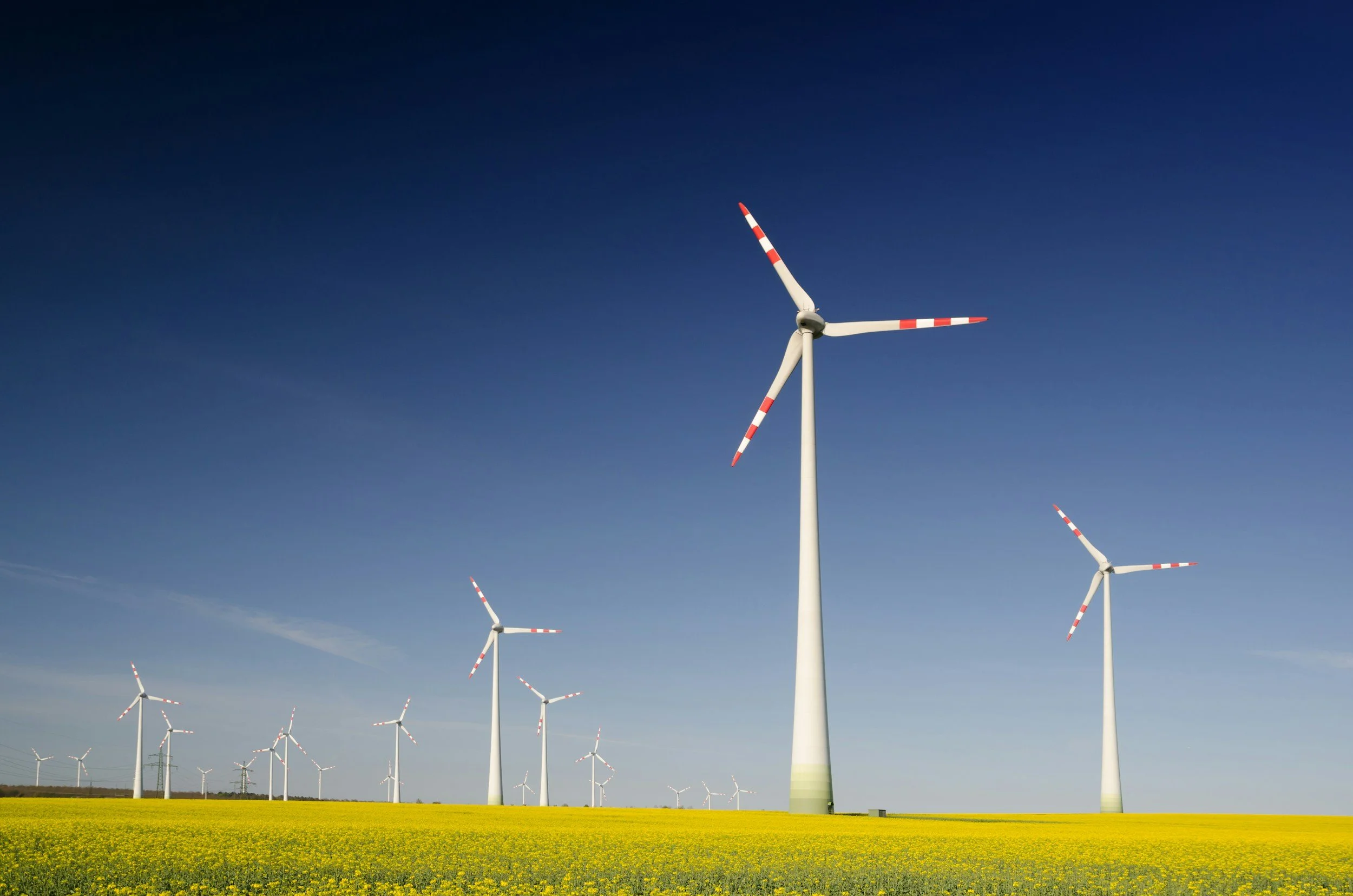
Sustainable Procurement Policy.
Introduction
SENSEI acknowledges that sustainable procurement is a process whereby organisations meet their demands for goods, services, works and utilities in a way that achieves value for money on a life cycle basis in terms of generating benefits not only to the organisation, but also to society and the economy, while minimising damage to the environment
It is the policy of SENSEi to practice a continuous improvement approach to understanding and taking appropriate responsibility and due diligence for any adverse environmental, social, and economic impacts of its procurement process. In doing so, SENSEI shall consider impacts on a life-cycle basis and prioritise actions according to alignment with SENSEi values, impact, and compliance with any applicable regulations.
This Policy is adopted in order to align SENSEI’s procurement with its values and goals. In doing so, SENSEI seeks to harness the influence of its procurement to support markets for, and increase accessibility to, more sustainable goods and services.
This policy applies across all SENSEI operational activities, procurement, deployment and to all employees, suppliers and clients.
Policy Implementation
In order to practice a continuous improvement approach to understanding and taking appropriate responsibility for reducing the adverse environmental, social, and economic impacts of our procurement, this policy establishes the following implementation hierarchy:
Core Strategies. These establish overarching sustainable procurement strategies to implement over time. They provide value-aligned direction to consider during all operational planning and deployment activities and direction from which to build minimum requirements, best practices, and related implementation tools.
Leadership Opportunities. These are developed to identify opportunities for continuous improvement among our stakeholders. They identify how to go beyond minimum requirements to further reduce adverse impacts.
All. SENSEI employees shall review the Core Strategies and follow the minimum requirements when planning, procuring for, designing, developing, deploying projects, operational activities, developing asset management plans, writing product and service specifications or standards, procurement, contracts, and supplier due diligence and selection criteria.
Core Strategies
Core Strategies will be undertaken in conjunction with our sustainable procurement considerations, policy and processes. Prior to making new purchases, employees are also expected to consider the need for the purchase, opportunities to extend the life of the existing product or meet the operational need through a different means (e.g. renting vs. purchasing).
Utilise processes, technologies, products, or services that reduce consumption of natural resources or chemicals.
Invoke processes, technologies, products, or services that reduce waste.
Invest in energy and fuel-efficient products, services, and technologies that result in simple paybacks, based on Total Cost of Ownership.
Invest in processes, technologies, products, or services that reduce the sourcing and use of Carbon-Based Fuels.
Seek processes, technologies, products, or services that support a Circular Economy.
Seek processes, technologies, products, or services that support biodiversity and healthy, resilient natural habitats.
Seek out, specify, and purchase products with lower Embodied Carbon than the status quo.
Seek out, specify, and purchase products that minimize exposure of Substances of Very High Concern (SVHC’s) to people and the environment.
Substances of Very High Concern (SVHC): Substances that may have serious and often irreversible effects on human health and the environment. SVHCs are typically defined as those that have one or more of the following attributes:
Persistent, Bio accumulative and Toxic (PBT)
very Persistent and very Bio accumulative (vPvB)
very Persistent and Toxic (vPT)
very Bio accumulative and Toxic (vBT), or known or likely to be:
Carcinogenic
Mutagenic
Reproductive or developmental toxicant
Neurotoxicant or Endocrine disrupting.
Seek out processes, technologies, goods, or services that support transparency in either or both SENSEI’s supply chain or product disposal endpoints regarding compliance with environmental regulations and Core Labor and Human Rights in the Workplace.
When using social or environmental product labels, seek out social/ecolabels that demonstrate that the product or service was independently certified to a reputable third-party environmental and/or social product or service leadership standard, preferably a multi-attribute standard that evaluates products or services along their entire life cycle.
Whenever possible, utilise Life Cycle Costing methods to determine the full cost of a product, service, or design
Minimum Requirements and Leadership Opportunities
Minimum requirements and associated Leadership Opportunities for a specific goods or service category shall be defined and communicated through SENSEI’s sustainable procurement process. This sustainable procurement process shall be maintained and updated accordingly to keep content current, accurate and relevant. Minimum requirements shall be based off well-researched and tested practices that are readily accessible and have been confirmed to reduce an adverse impact when well-implemented.
SENSEi Management is ultimately responsible for ensuring that this policy conforms with legal and ethical commitments. SENSEI Management is in charge of implementing this policy on a daily basis, monitoring its usage and effectiveness, managing lessons learnt, effective and measurable SLA performance reporting, breaches, awareness, communication, reporting, and quality assuring internal control systems and processes ensuring their accuracy and relevance.
SENSEI Management, at levels, is responsible for ensuring that direct reporting employees, consultants and suppliers understand and comply with this policy.
SENSEI ensure the sustainable procurement policy and processes are reviewed periodically, accessible to all employees, are made clear in our staff onboarding and refresh training, measurable in our internal SLA’s, reviewed in employee appraisals and included in all supplier contracts and contract / performance reviews.